Building Statistics
Building Statistics
Building Name: Earle Hall - New Residence Hall (East Halls)
Building Location: 134 Johnston Commons, University Park, PA
Occupant: The Pennsylvania State University
Occupancy Type: Residential Group R-2
Total Square Footage: 95,737 SF
Number of Stories Above Grade: 6
Dates of Construction: March 2016 - August 2017
Project Delivery Method: Design - Build
Approximate Cost: $35 Million

Construction Team
Owner: Penn State University
Architect: Mackey Mitchel Architects
Construction Manager: Clayco
MEPFPT Engineer: Barton & Associates
Structural Engineer: Hope Furrer Associates
Civil Engineer: Sweetland Engineering & Associates
National Model Code(s)
Pennsylvania Uniform Construction Code – 2009
International Building Code 2009
International Mechanical Code 2009
International Plumbing Code 2009
International Energy Conservation Code 2009
International Electric Code and National Electric Code (NFPA 70)
International Mechanical Code 2009
Zoning
Penn State University Planned District
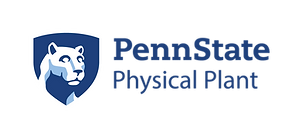
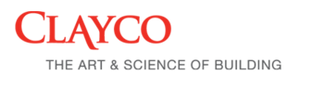

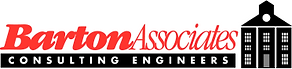

Architecture
The design of the New Residence Hall compliments the typical look of many Penn State buildings. The base of the exterior walls features a cast stone accent, while the rest of the walls are brick veneer. There is a curtain wall system in the main lobby and study area that expands to the building’s roof level. The inside of the building features high end finishes and furniture for student use.


Building Enclosure
There are two typical wall details that make up the building enclosure:
Brick Veneer:
Face Brick
Rigid Insulation
Air Barrier
Vapor Barrier
Plywood Sheathing
Metal Stud Walls
Curtain Wall System
The sections where the curtain wall meets the wall base and flooring assembly are shown below:
Curtain Wall System at Wall Base
Curtain Wall System at Floor Connection



Roofing
The roofing system in composed of a Thermoplastic Polyolefin (TPO) system that sits on 5/8” gypsum wall board insulation (R-Value min. R25).


Systems
Construction Means and Methods
The cold-formed metal panel system is an element of construction that utilized pre-fabrication. This system arrives to the site pre-assembled, numbered, and sequenced. This pre-fabrication helps to accelerate the construction of each floor stud wall and reduces waste. It also helps to increase worker safety on-site as the processes and materials for on-site stud construction are eliminated. Figure
Both a mobile and tower crane were utilized for on-site construction activities and phasing. The tower crane is a self-erecting crane that lifts itself into place using a series of jacks. Additionally, mobile cranes are utilized in various locations to lift the heavier loads that the tower crane cannot lift such as block pallets and large structural members. Extra precaution was taken to ensure that when the two cranes were both operational, and their paths did not intersect.
Structural System
The foundations of the New Residence Hall consist of both spread and strip footings designed to have a net bearing capacity of 6000 PSF. Rock anchors, near the stair and elevator shafts, work like micro-piles to tie the structural system to the dense rock below. The basement level is made up of reinforced concrete and CMU foundation walls. Columns, ranging from sizes W10X12 to W10X88, can be found on the basement and first floor levels. The rest of the structural frame is load bearing, cold-formed structural stud walls. Cold-formed metal joists carry the load of each elevated slab. A typical elevated slab of the building is composed of 1 ½” form deck with 4 ½” normal weight concrete (3500 PSI) reinforced with 6X6-W2.1XW2.1 draped, welded wire reinforcement. The building has two stair towers and an elevator shaft composed of 10” CMU that run from the basement to roof. The roof system is a Thermoplastic Polyolefin (TPO) system that is supported by the structural cold-formed metal joists.
Mechanical System
The mechanical system for the New Residence Hall implements both fan coil units (FCU’s) and energy recovery unit (ERU’s) in its design. The fan coil units supply heated and cooled air to each student housing unit and all the public spaces. There is one FCU for each mechanical zone. The FCU’s are fed by a 4-pipe system that incorporates hot, cold, and condensate lines. This fan coil system allows for individual control and less energy is devoted to air movement. The other element of the mechanical system is the energy recovery units. There are a total of 2 ERU’s, one for each wing of the building. The ERU’s work by taking 7600 CFM of 100% outside air and recovering energy from the exhaust air. They supply the public spaces and corridors of the building with conditioned ventilation. The bathrooms have all of the exhaust air in the building. The exhaust balances the building pressurization and is used in the ERU. There are also fin tube radiators for added occupant comfort near large glazing elements. For the individual rooms ventilation is provided from the corridors ventilation supply and natural ventilation through the windows.
Lighting
2’X2’X2 ½” recessed LED troffers are utilized to provide light for all of the buildings corridors. Each dorm has one, 1’X4’X3” surface mounted LED flat panel fixture that provides light to the entire room. The common bathrooms also feature a similar surface mount LED fixture. The lobbies and common spaces of the New Residence Hall are lit by 3”X6’X5” lensed LED slot fixtures. The use of LED lights bring many benefits to the building’s lighting system including long bulb life and increased energy efficiency.
Electrical
High voltage power is fed to the building, underground through a 4” conduit utility ductbank, from Findlay Commons. This power steps down to the main distribution panel switchboard and provides power at 277/480V, 100A. From here, power is fed to the electrical panels after leaving the secondary distribution switchboard. This secondary switchboard supplies power to the building at 120/208V, 3PH, 4W, 1200A.
Fire Protection
The building is fully equipped with a quick response, automatic fire sprinkler system. This is a wet pipe system hydraulically designed to provide 0.2 GPM/SF of water to the designated area.
Fire extinguishers are placed throughout the building at a maximum distance of 75 feet apart. Smoke alarms are present in all dorm rooms as well as public spaces.
The structural frame, bearing walls, and floor construction is designed to have a 2 hour fire rating. Roof supports and roof construction have a 1 hour fire rating.
Transportation
The New Residence Hall is equipped with two stair towers and one elevator shaft. The elevator and stair shaft walls are constructed of 2-hour rated, 10” CMU blocks. Both the stairs and elevators are designed for use by building occupants and employees. In an emergency situation, the stairs are the primary means of egress. The elevator is also equipped with a smoke containment system.
Telecommunications
Originating from the basement telecommunication room, 4 sets of telecommunication systems expand to each floor of the building from the telecom main grounding busbar. These systems bring CATV, telephone, data, and wireless access points to their respective locations and provide their services to their respective zones.